An idle air control valve controls the idle speed of an engine by managing the amount of air allowed into the engine when the throttle is closed. Typically, it is a simple solenoid that opens and closes a needle valve; blocking and unblocking an air passage.
IAC valves lie in the middle ground of modern engine development. On older carbureted engines, they weren’t used. Idle was controlled by a set screw that held the throttle plate open a certain amount.
The IAC valve is usually located on the intake manifold near the throttle body if it is present and is normally readily accessible and easy to replace.
Costs of Replacing an Idle Air Control Valve
For some average idle air control valve replacement cost on common vehicles, using $100 an hour as a labor rate:
- On a 2004 Kia Optima with a 2.4-liter engine, the estimated labor time is around 0.4 of an hour. For the replacement part, an OE would cost around $199 and a Standard is about $85. The total job cost for each would be $239 using factory parts and $125 using aftermarket parts.
- On a 2000 Volkswagen Passat with a 2.8-liter engine, the estimated labor time is around 0.5 of an hour. A Standard replacement part would cost around $138. The total job cost would be about $188 in this instance.
- On a 2003 Chevrolet S10 truck with a 4.3-liter engine, the estimated labor time is around 0.5 of an hour. For the IAC valve cost, an OE replacement part would be around $180 and a Delphi would be around $59. The total job cost for each would be around $230 using factory parts and about $109 using aftermarket parts.
- On a 2000 Nissan Maxima with a 3-liter engine, the estimated labor time is around 1.4 hours. For the replacement part, an OE would cost around $325 and a Hitachi would be about $112. The total job cost for each would be around $465 using factory parts and about $254 using aftermarket parts.
Cost savings for an idle air valve replacement, like many other running items, would mostly revolve around having an accurate diagnosis in the first place. The part itself is pretty simple and usually, physical inspection and an attempt to clean the valve would be a part of the diagnosis.
What Goes Wrong With Idle Air Control Valves
When fuel injection replaced the carburetors, the fuel-injected engines had a mechanical throttle body operated by a cable from the gas pedal. These required an IAC valve controlled by the engine management computer to maintain idle speed under all various conditions.
Most modern vehicles no longer use a throttle cable. Instead, they have an electronic throttle body directly operated by the PCM. In this type of system, the PCM is can manage the idle speed by fine adjustments of the throttle plate itself; eliminating the need for a separate valve.
An idle air control valve can fail mechanically or it can fail electrically. In a mechanical failure, the most common thing is for the valve to become dirty; in which case, it no longer seals when closed.
It can also become gummed up which interferes with its ability to smoothly open and close. A throttle body is subject to the same kind of problems. For the same reasons, the airflow into the engine isn’t perfectly clean and dry and fine debris can build up.
A first remedy is often to clean the air intake system with solvents. If this doesn’t help (and sometimes valve passages can be very difficult to clean), then, replacement is usually recommended.
Electrical failure is usually simple to diagnose. The IAC valve is operated by an integral solenoid and like any solenoid, it is a coil of wire that creates a magnetic field when current passes through it.
Testing for a grounded, the shorted or open coil is within the abilities of most shops and if an electrical problem is found, the valve will need to be replaced. Modern manufacturing methods seldom allow successful disassembly and reassembly.
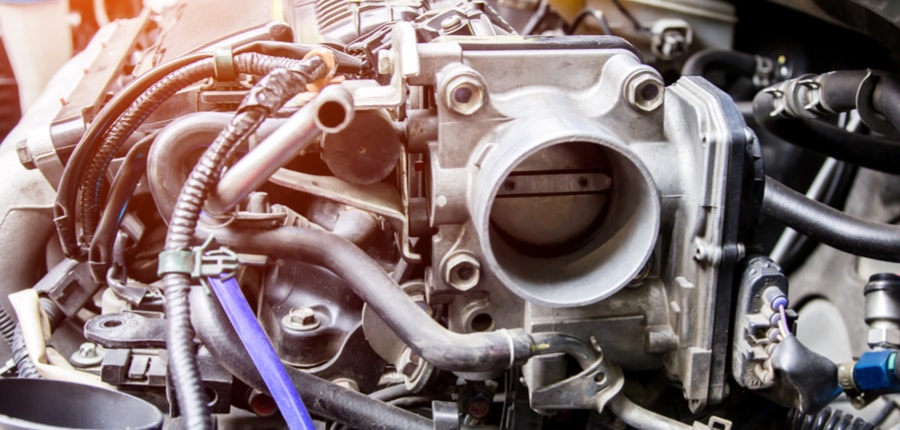
Other Issues That May Arise
The common symptom of a failing IAC valve is poor idle quality. Unfortunately, this is also a common symptom of failure for nearly everything else the engine depends on for smooth running: spark plugs and ignition wires, air filter, fuel quality, fuel injectors, the EGR system, numerous sensors the PCM uses data from, etc. Diagnosis can involve an hour of shop time; narrowing down and ruling out the various possibilities.
Sometimes, rather than going straight to diagnosis, a tune-up will be recommended if it’s suggested by the maintenance schedule. The scope varies by shop and vehicle but can involve the replacement of spark plugs and wires and cleaning of the intake system.
If this needs to be done anyway, it’s sensible to begin with it as the work rules out a number of things itself. Usually, during a tune-up, a sense of how the engine is running and what shape things are in can be gained which can guide further diagnosis if it’s needed.